Compressed air is a safe and reliable power source that is widely used throughout industry. Approximately 90% of all companies use compressed air in some aspect of their operations, however unlike gas, water and electricity; compressed air is generated on-site, giving the user responsibility for air quality and operational costs.
The problem with compressed air
Compressed air is not without its problems, with all systems suffering from performance and reliability issues. Almost all of these can be directly attributed to contamination. After generation, compressed air can typically have up to ten different contaminants present as it enters the distribution system and as modern production facilities become more complex and the applications for compressed air become more critical, the purification of the compressed air before use is essential.
The three sources of compressed air contamination
Atmospheric Air
Air compressors draw in huge amounts of atmospheric air, which continuously fills the compressed air system with contaminants such as water vapour, micro-organisms, atmospheric dirt & oil vapour.
The Air Compressor
In addition to the contaminants drawn in through the compressor intake, the compressor also adds contamination in the form of liquid oil, oil aerosols (lubricated compressors) and wear particles. The compressor after-cooler will also condense water vapour, introducing it into the compressed air in both a liquid and aerosol form.
Compressed air storage devices and distribution systems
As the air leaves the compressor it now contains eight different contaminants. The air receiver (storage device) and the system piping that distribute the compressed air around the facility can store large amounts of this contamination. Additionally, they cool the warm, saturated compressed air which causes condensation on a large scale adding more liquid and aerosol water into the system, promoting corrosion and microbiological growth.
The ten major contaminants found in compressed air
To many compressed air users, the realisation that there are ten main contaminants in a compressed air system is somewhat of a surprise. Many only think of water and oil as these contaminants are visual and are regularly seen to be causing problems.
The 10 contaminants are:
- Water Vapour
- Atmospheric Dirt
- Liquid Oil
- Micro-organisms
- Condensed Water
- Rust
- Oil Aerosols
- Water Aerosols
- Pipescale
- Oil Vapour
The largest quantity of contamination introduced into the compressed air system originates from the atmospheric air drawn into the compressor and not as often believed, introduced by the compressor itself. The most prolific and problematic of the contaminants is water which accounts for 99.9% of the total liquid contamination found in a compressed air system.
Contaminant removal
Failure to remove this contamination can cause numerous problems in the compressed air system, such as:
- Corrosion within storage vessels and the distribution system
- Blocked or frozen valves, cylinders, air motors and tools
- Damaged production equipment
- Premature unplanned desiccant changes for adsorption dryers
In addition to problems associated with the compressed air system itself, allowing contamination such as water, particulate, oil and micro-organisms to exhaust from valves, cylinders, air motors and tools, can lead to an unhealthy working environment with the potential for personal injury, staff absences and financial compensation claims. Compressed air contamination will ultimately lead to:
- Inefficient production processes
- Spoiled, damaged or reworked products
- Reduced production efficiency
- Increase manufacturing costs
The table below highlights each of the purification technologies required to remove the different contaminants present in the compressed air system.
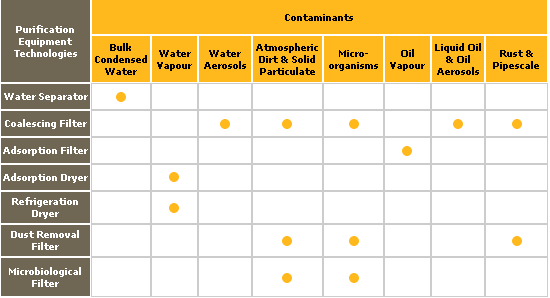